What are the Different Types of Industrial Material Handling Systems?
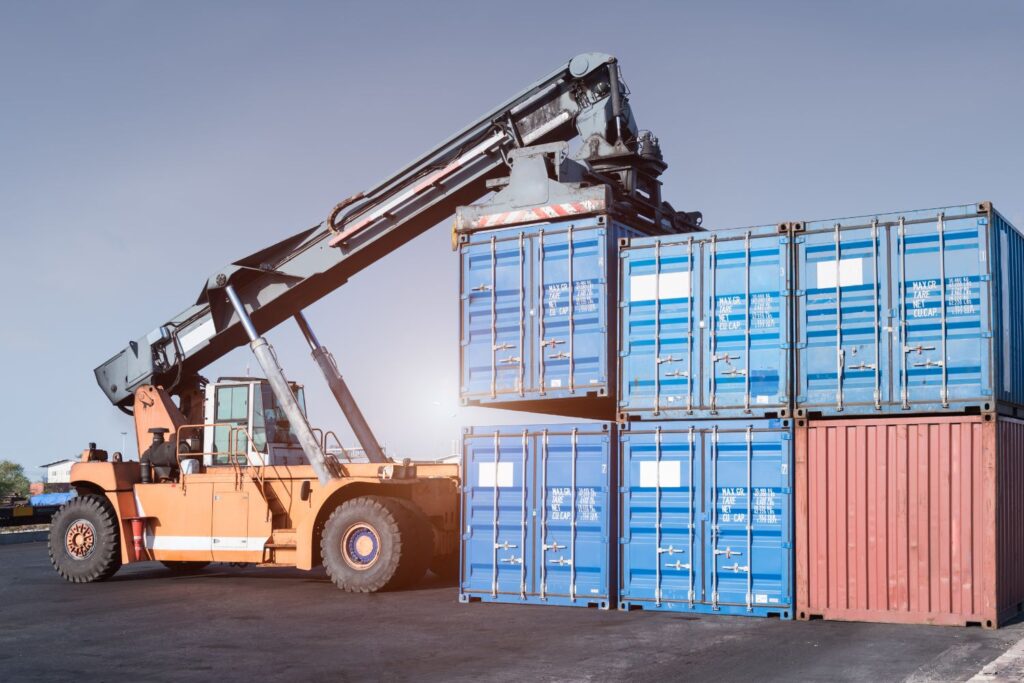
Proper material handling is required to avoid hindrances to productivity and increase the safety of employees in particular industries. In fact, according to research, effective material handling can improve overall operational efficiency by up to 30%. Regardless of your particular industry, ensuring that you have the right equipment will improve your warehouse or assembly line function.
Have you been searching for an effective material handling for use?
If so, then this detailed guide will indeed assist you in analyzing features, advantages, and usage.
What is an Industrial Material Handling System?
Material handling systems involve many types of equipment that are used in the manufacturing, disposal, receiving, and storing of goods. To ensure the longevity of using different material handling systems, it is important to select a system that suits a particular business and hence enhances productivity and cuts down expenses.
Types of Material Handling Systems
The types of material handling systems include:
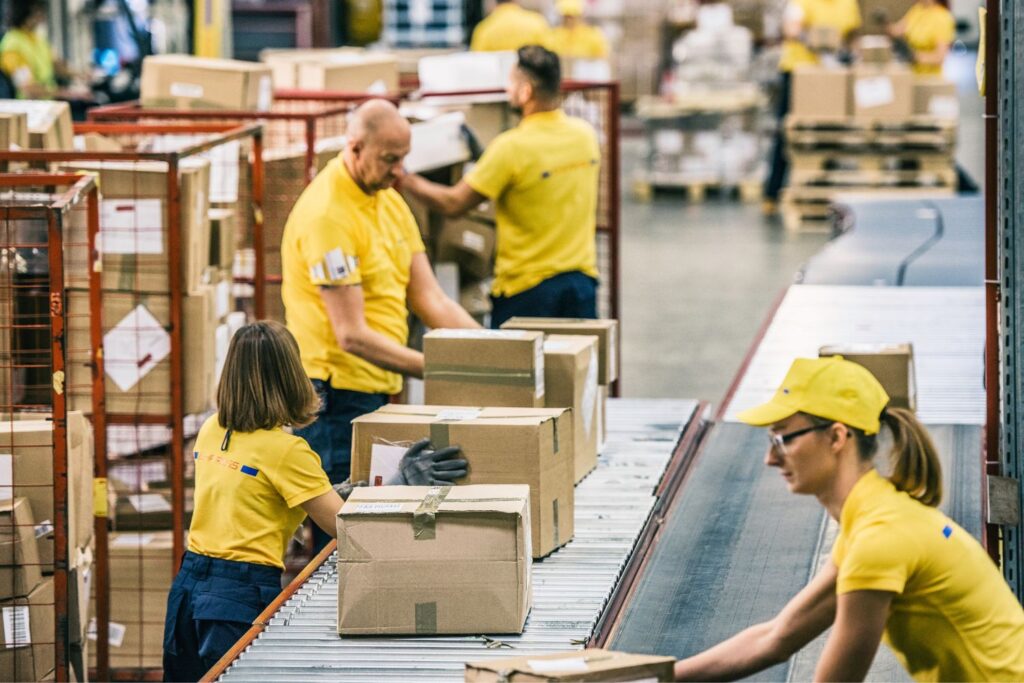
Bulk Material Handling Systems
Bulk materials handling systems are specialized equipment used for handling, transporting, and processing large volumes of materials in bulk, such as minerals, chemical and agricultural products. Common equipment in this category includes:
- Conveyors: A mechanical handling equipment that is used to move materials from one location to another. In transferring materials over short or long distances, conveyors can be used in the form of belt conveyors, roller conveyors and chain conveyors.
- Bucket Elevators: These are especially suited to applications in the vertical transport of crops such as grain and fertilizer.
- Hoppers and Silos: Both hoppers and silos are ideal storage containers that are particularly effective for handling large amounts of materials such as agricultural and mined products.
Industrial Lift Trucks & Forklifts
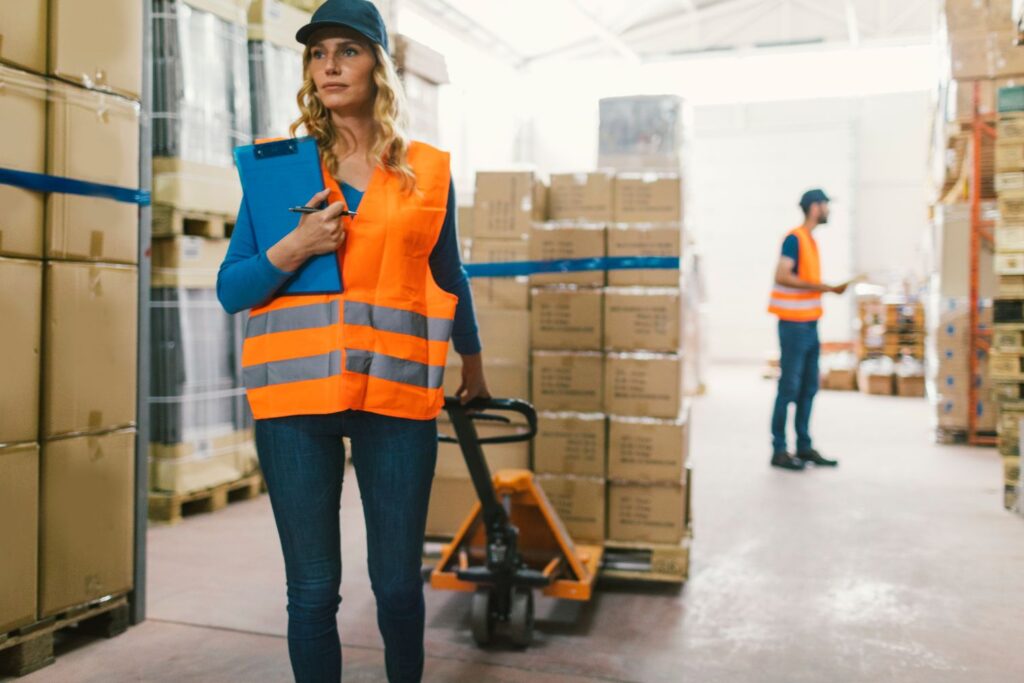
Industrial trucks are important equipment that are used in the movement, transfer and storage of goods. They come in various forms, including:
- Forklifts: Used in warehouses, forklifts are used to lift and move loads with capacities from as low as 3000 lbs to as high as over 30000 lbs. They are essential for loading, unloading, and transporting heavy or bulky materials in manufacturing, logistics, and construction settings. They come in various forms, like cushion tire forklifts, pneumatic tire forklifts, electric forklifts, and terminal tractors.
- Pallet Jacks: These are small dumper trucks which are either driven manually or by electricity, and are suitable for pallets’ shuttle in restricted or short distances.
- Order Pickers: These machines enable operators to select quantities from high shelves and increase picking efficiency.
Engineered Systems
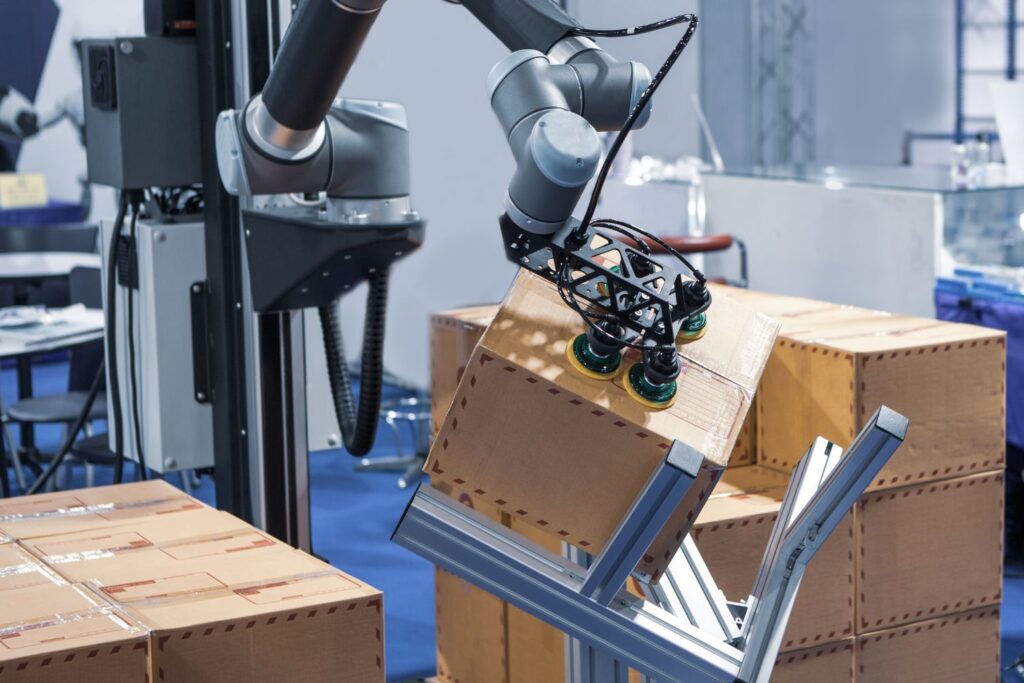
Engineered systems are physical systems and systems of control developed to reduce the use of manpower in the organization. Examples include:
- Automated Storage and Retrieval Systems (AS/RS): It employs robotic shuttles for order picking as well as for restocking in the high rack storage configuration.
- Automated Guided Vehicles (AGVs): Automated guided vehicles are another type well-suited for handling and moving parts and materials within a facility with the help of predefined paths.
- Conveyor Systems: These transport and handling systems control the mobilization of supplies through definite routes, thereby lessening the risk of manual intervention.
Storage and Handling Equipment
Storage equipment is meant to accommodate various resources. Key examples include:
- Pallet Racks: These racks optimize the ‘height’ factor and are mostly used hand in hand with forklifts and pallet jacks.
- Shelving Systems: Such storage systems are great for warehouses as they provide the ability to adjust for different sizes and types of items.
- Bins and Totes: Stationery as bin totes are used to arrange smaller items for sales and products and for easy stocking of inventory.
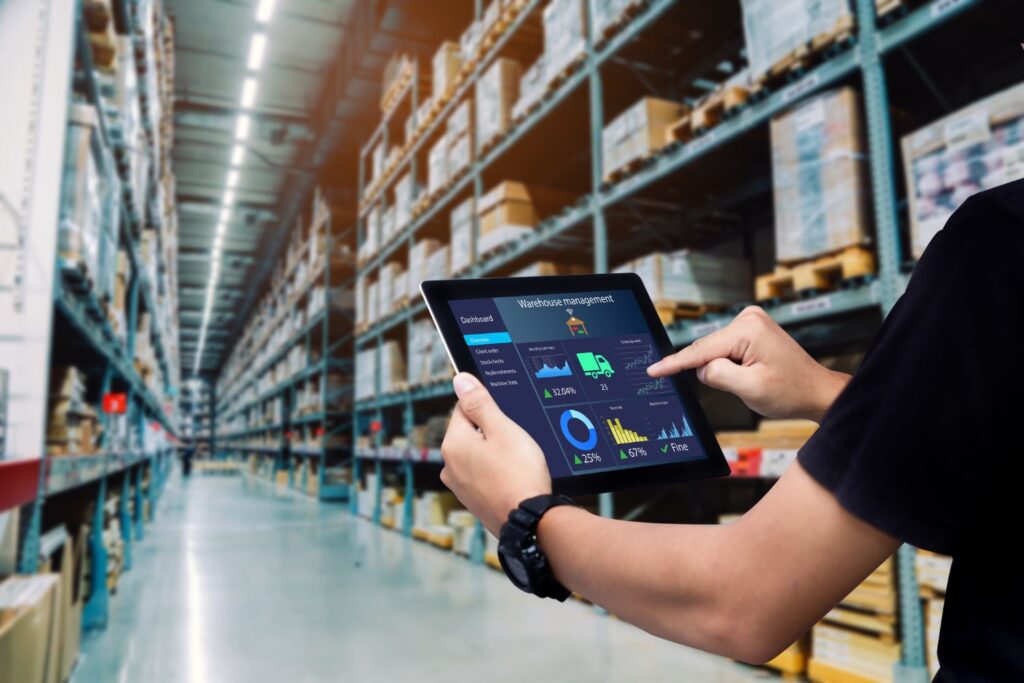
Benefits of Efficient Material Handling Systems
Implementing the right material handling systems offers several benefits, including:
- The cost of goods is increased by automated systems and efficient equipment since they take less time and labor handling for the movement and storage of materials.
- Appropriate handling equipment reduces the possibility of risks in terms of lifting and shifting of loads.
- With the set up of an efficient material transport system, the labor that is required for this type of transport is mostly reduced leading to an overall reduction in cost and damages on goods that are transported also minimized.
- Efficient management of stock storage implies the optimal utilization of the existing space, and it enables larger quantities of stock to be stored despite the limited physical space available.
Comparison of Material Handling Systems
System Type | Key Equipment | Primary Use | Benefits |
Bulk Material Handling | Conveyors, Bucket Elevators, Hoppers | Transporting and storing loose materials | High capacity, automation-friendly |
Industrial Trucks | Forklifts, Pallet Jacks, Order Pickers | Moving packaged goods within a facility | Flexibility, various load capacities |
Engineered Systems | AS/RS, AGVs, Conveyor Systems | Automated storage and movement | Reduced labor, increased speed and accuracy |
Get The Ease of Perfect Systems With Large Lift Trucks
Selecting the appropriate material handling system is important for optimizing industrial operations. By understanding the types of systems and their applications, businesses can enhance productivity, ensure safety, and achieve significant cost savings. Whether you’re dealing with bulk materials packaged goods or need automated solutions, there is a material handling system to meet your needs.
For more detailed information on specific equipment and solutions, consider consulting with a material handling expert at Large Lift Trucks to tailor the right system for your operational requirements.
Common Questions About Industrial Material Handling Systems
Q1. What factors should I consider when choosing a material handling system?
When selecting a material handling system, consider factors such as the type of materials to be handled (size, weight, and fragility), the volume of materials, the layout and space constraints of the facility, and the level of automation required.
Q2. How can material handling systems improve workplace safety?
Material handling systems can significantly enhance workplace safety by reducing the need for manual lifting and transporting heavy loads, which minimizes the risk of musculoskeletal injuries.
Q3. What are the maintenance requirements for material handling equipment?
Maintenance requirements vary depending on the type of equipment. Regular inspections, lubrication, and adjustments are essential for mechanical systems like conveyors and forklifts.
Q4. What are the environmental impacts of using material handling systems?
The environmental impact of material handling systems can be mitigated by choosing energy-efficient equipment and implementing practices that reduce waste. Electric-powered forklifts, for example, produce fewer emissions than their gasoline counterparts.
Q5. How can I optimize the layout of my facility for better material handling?
To optimize facility layout, consider the flow of materials from receiving to shipping. Use space efficiently by implementing vertical storage solutions like pallet racks.
Q6. What are the latest trends in material handling technology?
Recent trends in material handling technology include the increased use of automation and robotics, such as autonomous mobile robots (AMRs) and automated guided vehicles (AGVs). The integration of Internet of Things (IoT) technology and data analytics is also becoming common, allowing for real-time monitoring and optimization of material handling processes.
Q7. How do material handling systems support just-in-time (JIT) manufacturing?
Material handling systems support JIT manufacturing by ensuring that materials are delivered to the production line precisely when needed, reducing inventory costs and minimizing waste.
Q8. Can material handling systems be customized for specific industries?
Yes, material handling systems can be customized to meet the unique needs of various industries. For example, the pharmaceutical industry may require cleanroom-compatible equipment, while the food industry might need systems that comply with stringent hygiene standards.